Case Study: Achieving a High-Risk Systems Overhaul on an Accelerated Schedule
- gradymoore7
- Feb 26
- 7 min read
Updated: Mar 26

February 2025 — Based in Duncan, South Carolina, TGES America opened its doors in 2015 as a subsidiary of Tokyo Gas Engineering Solutions Corporation, a global engineering and energy solution provider with more than 50 years in the energy industry. In addition to EPC services, TGES America offers U.S. industrial customers onsite energy services, for which TGES America owns the plant facilities that provide electricity, steam and other utilities needed for production.
Known in aggregate as a central utilities plant (CUP), TGES America operates these facilities for customers on leases running 20 years or more. TGES America can also negotiate long-term power agreements with external utilities, including solar and other renewables so plants and the firms owning them can meet their net-zero decarbonization goals.
The TGES America model eliminates the capital expenditure and helps to level operating expenses that its customers would otherwise incur in owning and maintaining those facilities themselves while simplifying plant budgeting and planning. It also allows plant management to focus more on meeting production goals and delivery commitments.
The Challenge | Introducing a state-of-the-art and reliable control system early to enhance customer satisfaction
One TGES America customer is a specialty materials manufacturer. The plant’s CUP provides steam, compressed air, chilled water, deionized water and cooling water, all of which are required by several production lines for their many sophisticated and carefully calibrated processes that ensure maximum efficiency and yield.
When TGES America took on responsibility for the plant’s CUP several years ago via a long-term lease, it became apparent that the existing control system needed to be upgraded to ensure greater stability. “We quickly realized upgrading the system was necessary to consistently meet our customer's requirements,” says TGES America CEO Konosuke Usui.”
TGES America decided to develop and deploy a more advanced and highly reliable industrial control system (ICS). Moreover, given that CUP energy service agreements typically span 20 to 30 years, the ICS needed to be future-proofed for such a long lifecycle and be upgradeable with the latest technologies over that time.
The Solution | Engage an expert partner to design, engineer, and install fully modern and ultra-reliable systems for CUP controls and monitoring
In 2019, TGES America began searching for solution providers. Familiar with Siemens' reputation for high-quality and reliable automation and controls, TGES America's project team used the Siemens Partner Finder to shortlist potential system integrators.
After carefully evaluating five candidates, TGES America's project team chose aeSolutions, a 120-employee systems integrator based in Greenville, South Carolina, with offices in Houston and Anchorage. As a certified Siemens Solution Partner, the company specializes in solving extreme industrial engineering challenges in process safety, combustion control and safeguarding, safety instrumented systems, control system design and integration, alarm management, and related operations and integrity management systems.
“aeSolutions stood out from the others with their excellent response and superior technical proposal, which made them the clear choice for assisting us in the critical overhaul of our customer’s CUP facilities,” Usui says. “We also knew we could trust the highly integrated Siemens technologies included in aeSolutions’ proposal.”
Solution Designed - Cold Cutover Planned
In December 2020, TGES America‘s Project team awarded aeSolutions an initial contract to allow for preliminary engineering and for the early purchase of equipment due to the global pandemic extending supply chain deliveries.
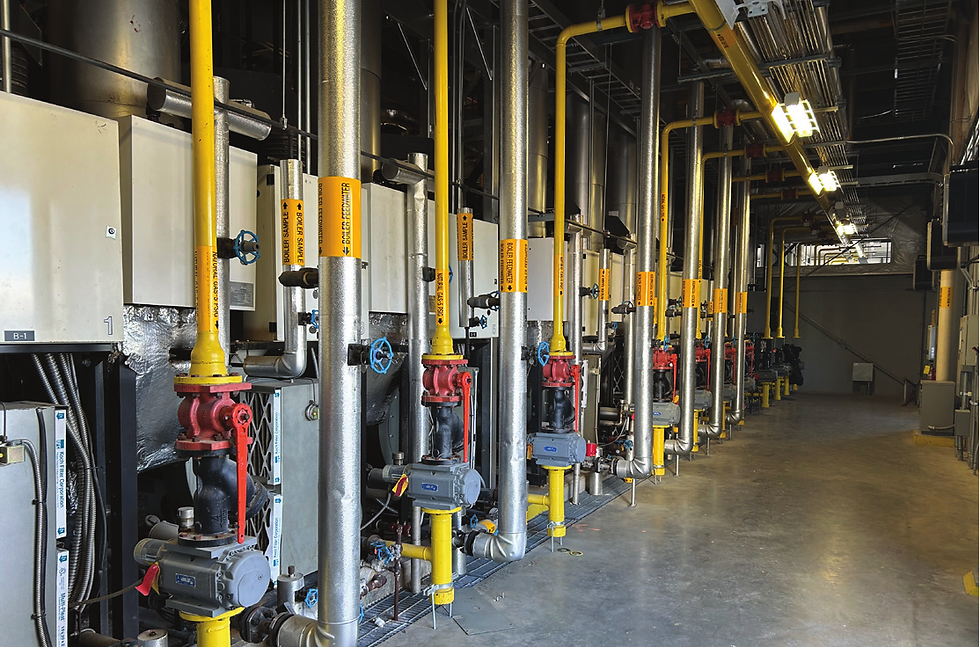
“At that time, the project had a completion target of March 2022,” aeSolutions CEO Ken O’Malley recalls. “The production facility was idle due to the pandemic, so the project’s execution plan would allow for an extended cold cutover to the new control system.”
His engineering team worked closely with TGES America’s Project team to develop a comprehensive ICS solution consisting of these Siemens components drawn from the Totally Integrated Automation (TIA) portfolio:
SIMATIC S7-1500H Programmable Logic Controllers (PLCs), which provides the CUP with high availability and built-in redundancy via a backup CPU synchronized with the primary CPU to ensure continued operation with no data loss. It also features built-in diagnostics with highly secure remote accessibility from anywhere at anytime by any web-enabled device.
SIMATIC ET 200SP Distributed IO, a scalable and highly flexible system for connecting process signals to the S7-1500H PLC over high-speed PROFINET.
SCALANCE Layer 2 Managed Switches, for securely segmenting the plant network that supports the CUP’s many physical utilities and their production process- enabling functions.
WinCC Runtime Professional V17, a PC-based operator control and monitoring system for visualization and operation of all the CUP’s processes, production sequences, and connected machines across the plant.
SCALANCE Industrial Ethernet Security Appliance, for secure remote access to the control LAN.
The Siemens TIA Portal was used to program the CUP’s control system as well as its WinCC Professional HMI. The TIA Portal’s intuitive, all-in-one software engineering platform with a drag-and-drop interface unifies control programming, HMI visualization development, and parameter settings. “With TIA Portal, our engineers saved time and delivered higher quality with less effort versus other ICS platforms because of the totally integrated architecture,” O’Malley says.
Schedule Accelerated by Four Months - Hot Cutover Required
In March 2021, Usui recalls, the customer told TGES America that the global pandemic was easing and that there was a change in the customer's production schedule, meaning the plant would be ramping up to full production four months earlier than originally planned. “So, after considering how much our project team could pull in the various engineering, procurement, testing, and commissioning tasks involved, we agreed to a new target completion date,” he says.
But this accelerated timeline didn’t come without execution risks, according to O’Malley. “Because the production facility’s ramp-up would be well underway when the new date for the new control system cutover would happen, we’d have to perform it hot without interrupting the plant’s utilities supply to production,” he says. “Clearly, doing this would be no small feat.”
In such challenging circumstances, TGES America project manager Atsushi Iwamoto and aeSolutions project manager Shane Kjergaard worked closely together, repeatedly revising the project plan and tirelessly coordinating with stakeholders to ensure the project stayed on schedule. As a result of the TGES America and aeSolutions teams coming together as one team, they were able to achieve completion on the revised schedule.
In addition, aeSolutions’ engineering team is very experienced completing complex hot cutovers, for example, the hot relocation of a large control room in the Artic for one of the world’s largest natural gas processing plants.
“In the end, we managed a complex, step-by-step hot cutover plan of the control system without interrupting the plant’s utilities supply,” O’Malley says. “The easy Siemens component integration and TIA Portal programming took systems integration off the critical path so we could focus on executing the hot cutover.”
For that, aeSolutions developed an interim hybrid control architecture using the site’s existing Modbus TCP/IP network to share signals between the old system and the new Siemens ICS. “Think back to hard-wired signal switches,” he explains. “As we moved the signal wires from the old system to the new Siemens ICS, the old system still had access to those signals via Modbus. Once most of the signals for a given system had been moved over to the Siemens system, we switched master control for that system over to the Siemens ICS. It was a tightly coordinated, high-stakes dance with operations, construction, and engineering all working together.”
Results | Improved Margins and a Repeatable Reference Model for TGES America — With Reliable Plant Utilities and Customer Trust Restored
Now, Usui reports the Siemens ICS is working reliably and to specification. TGES America has improved efficiency and successfully enhanced the operational stability of the plant. “Our customer is satisfied, so we are quite satisfied.” he says. “Our successful ICS solution provides us with a repeatable reference model for other customers. And it’s one we can quickly configure to their specifications while saving custom engineering time and costs.”
Usui adds ,“The Siemens PLC’s built-in diagnostics enable onsite operators to quickly troubleshoot and remedy issues before they impact production. And if an escalation is required, aeSolutions or Siemens experts can remotely access the system using the Siemens SCALANCE security appliance with TIA Portal to do the troubleshooting and remediation themselves, minimizing downtime.”
Future-Proofed for Decades to Come

What’s more, the advanced Siemens technologies inside the ICS provide much greater operational visibility, so TGES America can conduct condition monitoring for preventive and even predictive maintenance of plant facilities. “As we expand our TGES America customer base, we can extend this visibility and monitoring across all of our deployments to manage them as a fleet and keep watch on each site’s performance,” Usui says.
TGES America and aeSolutions are also discussing whether they can pursue even greater stability by introducing new technologies. “For example, the new AI tools coming available for our customers today are exciting, such as Siemens S7-1500 TM NPU module that operates using a trained neural system,” says O’Malley. “It’s literally a plug-and-play upgrade and, with it, the CUP’s different utility provisioning systems can read their own sensor data, intelligently interpret performance variations and anomalies, then respond flexibly and automatically to situations that used to require manual intervention, reducing downtime and increasing availability.”
This kind of Siemens technology advancement gives Usui the confidence to know that when TGES America deploys a control system, its lifecycle will span the long-term leases that are the basis of the TGES America business model. “At the same time, we expect our strategic partnership with aeSolutions and their expertise, experience, and tight relationship with Siemens will help us continue to prosper and help our customers be successful for many decades to come,” he says.
Comments