PSM and RMP Audit Themes Across Industry Part 1
- beckykramer7
- Oct 25, 2022
- 4 min read
Updated: Feb 19, 2024
by Judith Lesslie, CFSE, CSP
Those who work in high hazard industries are familiar with the OSHA Process Safety Management (PSM) and EPA Risk Management Plan (RMP) requirements for routine audits to assess and verify compliance with these regulations. In a prior blog, we reviewed different strategies for accomplishing these audits. In this blog, we will cover specific types of concerns that have been identified at many manufacturing sites.
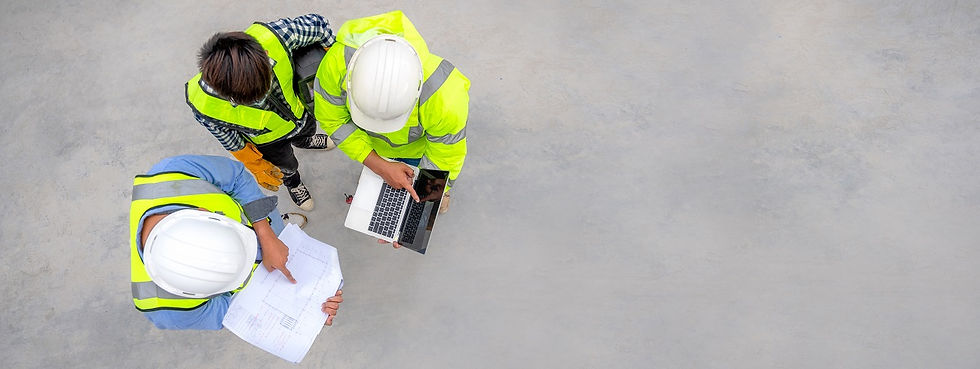
The Challenges
Companies conduct audits in order to assess the effectiveness of their process safety systems, with the primary goal of ensuring their covered processes are managed in a way that minimizes the risk of process safety incidents. In a review across many manufacturing segments, company, and site PSM and RMP audits, it has been found that the same types of concerns are present at many locations. These areas of concern occur across the entire range of PSM and RMP elements. In Part 1 we discuss PSM/RMP applicability, Employee Participation, Incident Investigation, Contractor Management and Hot Work, Emergency Response and Audits:
In the area of PSM and RMP applicability, it is important for sites to assess and document their inventories of highly hazardous chemicals (HHC), keeping in mind that the PSM and RMP HHC lists are not identical. In a related vein, failure to analyze HHC inventories near occupied buildings and failure to completely assess interconnectivity of potentially covered process equipment can be serious concerns.
Employee Participation is an important element of compliance. While most sites have a reasonable level of employee participation in their process safety programs, that participation is often not described in a procedure or road map. This represents a missed opportunity to document participation and to educate site personnel on their opportunities to get involved in process safety activities.
Sites often have a one-size-fits-all Incident Investigation method, which may be either too simple or too complex for some incidents; this leads to the potential for missed root causes that need to be addressed or to spending too much time and effort on less severe incidents. Allowing for a range of investigation methods depending on the actual and potential severity of an incident is an excellent practice to consider.
Management of Contractors is typically reasonably good across sites, with the possible exception of failure to consider past performance of contractors in ongoing selection processes. A process to define acceptance criteria and to assess past performance of contract firms via review of their OSHA logs is sometimes found to be a concern.
One would think that compliance with the Hot Work element would be simplest of all since the requirements are clearly and prescriptively outlined in OSHA 29 CFR § 1910.252. Two of the most frequently identified concerns for this element are failure to maintain or document a fire watch present for 30 minutes after any welding or cutting operations. The other is failure to post additional fire watches on multi-level worksites where falling sparks may be a concern or conduction, or radiation may pose a concern to combustibles that cannot be removed or protected.
Emergency Response is an area where the PSM and RMP standards diverge to some extent, including the distinction between offensive and defensive responders. Compliance with the PSM Emergency Response element is relatively straightforward and largely covered in 29 CFR 1910.38 - Emergency action plans. Where concerns are more often identified is in the RMP Emergency Response element, where the outward-looking activities are not always in perfect order. For example, all affected public receptors may not be identified and documented in the site emergency procedures, and/or the contact information for those receptors may not be tested on a regular basis. While not specifically a PSM or RMP requirement, the incident management plans for some companies do not take advantage of structuring their incident management systems in accordance with the National Incident Management System (NIMS); there is valuable free training offered through FEMA which will qualify site personnel to act in standardized ICS roles and enable good coordination with outside agencies in the event of a serious incident.
Audits are deserving of their own blog article (which you can find here). The most common audit element theme found at various facilities is an audit that does not dig deep enough into process safety programs and into the evidence of execution of each program element. Audits are overdue more frequently than you might anticipate as well. When a good-quality periodic audit with actionable recommendations is executed, that is not the end of the process. The recommendations or actions from that audit then need to be tracked to completion and documented as complete in a reasonable period of time, and that is unfortunately lacking at a variety of facilities.
The Stakes
The PSM and RMP regulations have proven over time that they are excellent practices to drive the reduction of serious process safety incidents. It is far better for a company and sites to find and correct their own PSM and RMP system deficiencies than for a serious incident to occur or for a regulatory agency to identify it. Are you positive that the commonly found concerns reviewed above are not present at your facility?
So What?
If you have not previously taken a deep dive into the assessment of the topics above at your site, now would be a good time to do so. If you do not have the right expertise in your staff to assess PSM and RMP compliance in these areas, consider selecting a process safety consultancy with deep experience and expertise to assist you. Their range of experience enables external auditors to share the general methods proven to drive good PSM and RMP compliance across industry. This independence from the site and company has the best probability of a careful assessment with fresh eyes on the relevant critical systems and leads to more efficient compliance with the necessary standards.
Commenti