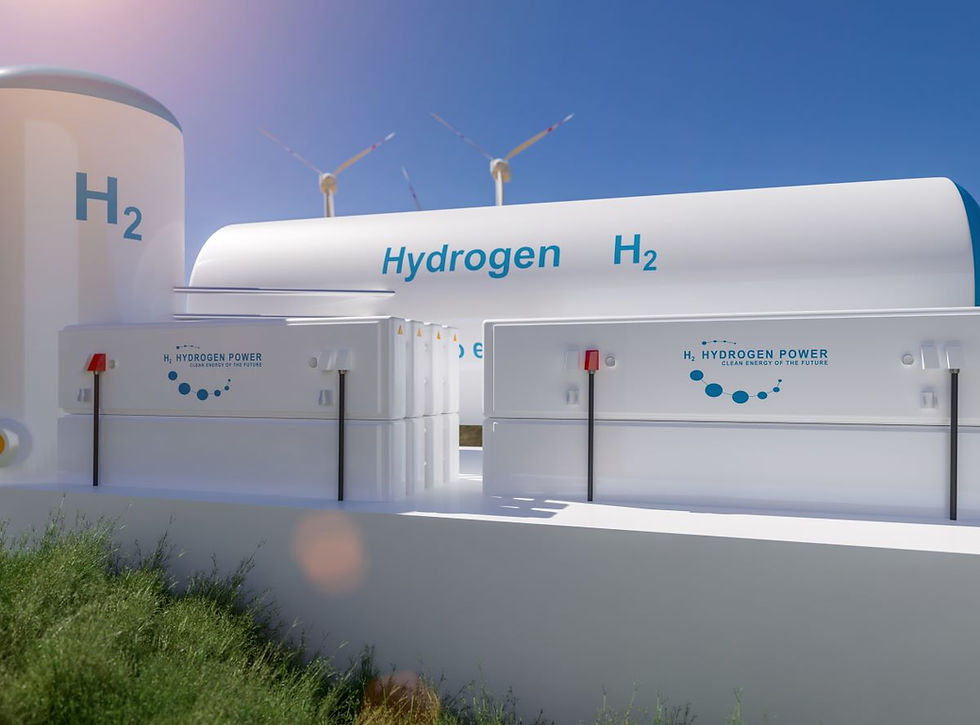
Designing and Implementing a Fire & Gas Detection System for a Hydrogen Production Plant

In the rapidly expanding field of hydrogen production and storage, safety is paramount. aeSolutions was presented with the complex challenge of designing and installing a fire & gas (F&G) detection system for a greenfield hydrogen production plant. This case study explores how aeSolutions overcame the unique hazards associated with hydrogen to create a robust and efficient detection system, ensuring the protection of both personnel and assets. Through a combination of advanced modeling techniques and strategic detector placements, aeSolutions delivered a solution that not only met safety requirements but also optimized system performance and cost-efficiency.
Challenge
aeSolutions was tasked with designing and installing a Fire & Gas (F&G) detection system for a new hydrogen production plant, which presented unique challenges due to the flammable nature of hydrogen. The plant included both indoor and outdoor processes, with hydrogen production occurring inside a ventilated building and other processes like filtration, compression, and storage taking place outdoors. The key challenge was to create an effective detection system that could handle the complexities of hydrogen's properties while ensuring the safety of personnel and the facility.
Solution
aeSolutions implemented a multi-step approach to optimize the gas detection system layout. The process began with preliminary geographic placements based on recognized standards and was followed by scenario-based placements using consequence modeling software. When initial models indicated uncertainties regarding potential explosion severity, aeSolutions employed Computational Fluid Dynamics (CFD) modeling to refine detector placements, reducing the number of detectors required while ensuring comprehensive coverage. Additionally, the design included strategic placements of both catalytic bead and ultrasonic gas detectors indoors and outdoors to efficiently detect leaks and mitigate potential hazards.
Results
The final design resulted in a robust detection system that optimized the placement and number of detectors, ensuring reliable detection of hydrogen leaks with minimal risk of undetected releases. The CFD modeling confirmed that with proper mitigation measures, hydrogen leaks could be controlled, preventing catastrophic explosions. The project concluded with the successful installation of 18 lower explosive limit (LEL) indoor detectors and 7 outdoor detectors, along with additional safety features like ultrasonic detectors and flame detectors. This approach not only enhanced safety but also minimized system costs and maintenance needs, providing a scalable solution for this hydrogen production facility.
Industry: Hydrogen
Geography: Southeast
Unit Operation: Hydrogen production including the use of electrolyzers